Stage I Vapor Recovery
These tests are designed to verify the integrity of pressure-vacuum vents installed on USTS and to confirm that vapor systems comply with specific static pressure regulations.
One of the most recent regulatory requirements for UST facilities is the EPA’s National Emission Standards for Hazardous Air Pollutants, better known as NESHAP. This new regulation, intended to help minimize the fuel vapors released from a fueling facility, requires most operators to conduct regular Stage I Vapor Recovery testing at their sites. These tests verify the integrity of pressure-vacuum vent valves installed on USTs and confirm that vapor recovery systems comply with specific static pressure requirements. Fueling facilities in an EVR County or with at least 100,000 gallons per month in throughput and new facilities must be in compliance at start-up. Thereafter, systems must be tested every three years.
Our Testing Services include:
-
- Pressure/Vacuum Vent Cap Testing
- A technician will perform a vent cap test, using our pressure/vacuum vent cap tester, per CARB TP-201, E, and install new compliant PV caps, as necessary.
- Pressure Decay Testing
- A technician will perform a 2-inch pressure decay test, per CARB TP-201.3.
- Drop Tube Length Inspection & Verification
- A technician will inspect and verify that the drop tube inside the tank is installed to within the specified distance of the tank bottom.
- Pressure/Vacuum Vent Cap Testing
Secondary Dri-Sump Containment Testing
Secondary containment systems provide important protection from leaking components in a fueling system. Product leaking from sumps, pipes, dispenser pans or spill buckets could result in substantial damage to the environment and potentially the drinking water supply.
Product leaking from sumps, dispenser pans or spill buckets could result in substantial damage to the environment and potentially the drinking water supply.
Secondary Containment Systems provide important protection from leaking components in a fueling system. Testing of secondary containment systems helps ensure that the systems in place to contain any leaking product are working as designed to prevent fuel from escaping into the ground. Not only is this testing an important part of your environmental compliance plan, but it’s also a great risk management practice.
At EPS, we use an innovative technology called Dri-Sump Containment Testing that meets the technical requirements of tank and sump manufacturers. Dri-Sump Containment Testing is a vacuum test method designed for all types of containment sumps and spill buckets. It takes little time, uses no water and creates zero waste, allowing you to quickly and safely test any open or closed top containment! Instead of using water, it fills the entire containment sump with heavy vapor aerosol, and then an air generator pulls the soil gases from around the sump and into a viewing chamber. Using a laser in this viewing chamber, a green laser line indicates a leak detected, whereas a dot indicates no leaks detected. The heavy vapor aerosol dissipates within ten minutes or less.
Some key benefits with our testing include:
No Site Downtime – Most sites can be tested in several hours, with minimal facility shutdown required.
No Site Waste – With our testing equipment, there is no wastewater generated.
Single Site Visit – Some other methods require a second site visit after 24 hours to ensure no water level change has occurred. We can test most sites in a single visit.
Dri-Sump Spill Bucket Testing
Spill containment buckets prevent petroleum products from being released into the environment in the event of a spill or overfill. Over time, exposure to fuel and weather can cause containment buckets to deteriorate and become a source of leaks which are often overlooked.
Spill containment buckets prevent petroleum products from being released into the environment in the event of a spill or overfill. Over time, if they are forgotten or overlooked, the exposure to fuel and weather can cause them to deteriorate and potentially leak.
Just like with our Sump Containment Testing, we use the Dri-Sump Method to test spill buckets. Our spill bucket testing service verifies that spill containment buckets continue to perform according to manufacturer specifications and can prevent leaking of products into the environment. If a spill bucket is found to be leaking, our service technicians can repair or replace it and test the system again, saving the time and expense of a return visit.
Benefits of our testing technology include:
- Innovative Approach: Our test verifies that the spill containment bucket continues to perform according to manufacturer specifications and will prevent a release of product into the environment.
- Accurate & Practical Results: Our technology provides extremely accurate results, in many cases identifying even the smallest leaks that would be missed by other methods. Best of all, it comes at a low cost per test.
- No hazardous waste generated: Our method of testing generates no hazardous waste. Other methods generate waste by-products that require special handling, resulting in higher test costs.
- Most Repairs available on the spot: Our cross-trained service technicians can quickly repair or replace a faulty component and immediately re-test the system – saving time, reducing facility downtime and reducing cost by eliminating the need for a second visit.
Tank, Line and Leak Detector Testing
We can perform verification tests on your entire UST system – tanks, piping and leak detectors – ensuring that the whole system is tight and free from any leaks.
Testing the key components of your underground storage tank (UST) system is one of the most important things you can do to reduce the risk of a fuel leak, which can cause catastrophic damage to the environment and put your business at serious risk.
EPS can perform verification tests on your entire UST system – tanks, piping and leak detectors – ensuring that the whole system is tight and free from any leaks.
Our tank testing technologies can be used on nearly any petroleum product, including tanks with varying amounts of fuel.
All our methods are third-party certified, in accordance with Federal EPA regulations and have been reviewed and approved by the National Work Group on Leak Detection. All work is performed by our expert technicians, and our emergency response service is offered 24/7, year-round. You can rest easy knowing that EPS is there to take care of your testing needs whenever they occur.
Available Services:
Tank Testing:
-
- Patented vacuum technology
- Certified for tanks up to 75,000 gallons
- Detection probability is 100%
- False alarm probability is 0%
Line Testing:
-
- Rigid piping certified up to 172 gal.
- Flexible piping certified up to 119 gal
Leak Detector Testing:
-
- LDT-5000™ is calibrated to detect 3 GPH leak at 10 psi
EPS Benefits
Proven Technology: Non-volumetric tank testing system is the world’s leading UST testing method.
Minimal Site Disruption: Most testing and repairs can be conducted within the same day, with a single visit.
Instant Access: All test results are maintained in our secure online customer portal, with easy access 24/7.
Compliance Testing Services
When it comes to compliance, Environment Petroleum Services has you covered! With accurate results, minimal disruption to your site operation and the best value for your money, partnering with EPS gives you the confidence that your site is protected and in compliance with the law.
Whether you need a total compliance program for your entire UST site, or the testing of a single component, we offer a broad range of compliance services. Our trained and certified technicians are available 24/7 to make sure you have the best service and coverage possible.
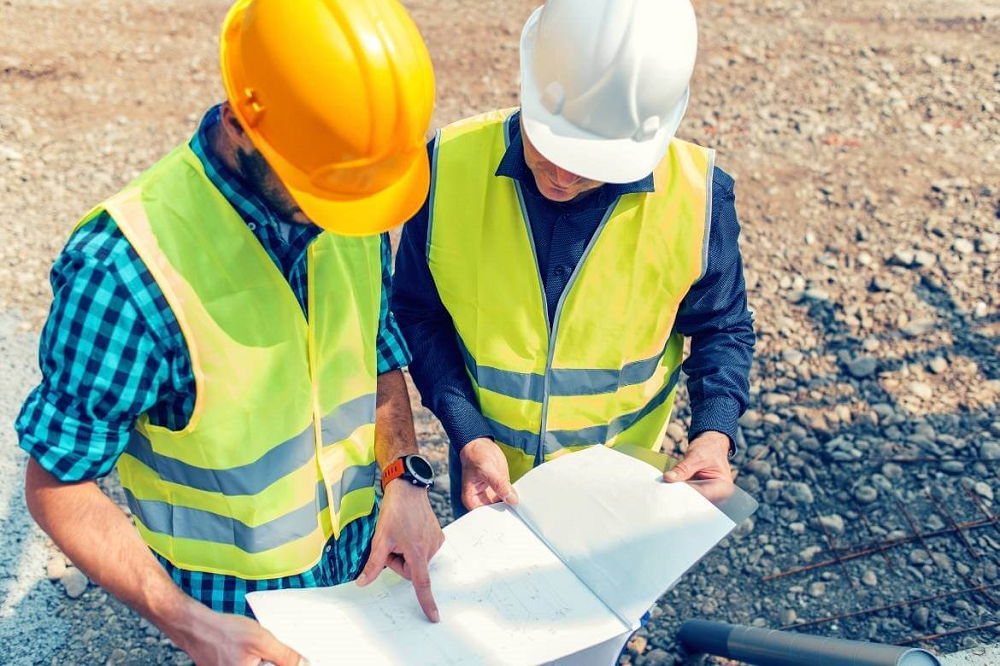